
An in-depth understanding of why concrete cracks and the types of cracks usually seen in concrete
What is Concrete
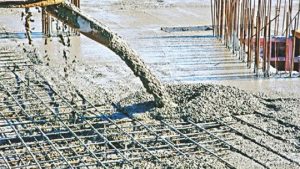
Concrete is a composite material composed of fine and coarse aggregate bonded together with a fluid cement (cement paste) that hardens (cures) over time. Concrete is the second-most-used substance in the world after water, and is the most widely used building material. Its usage worldwide, ton for ton, is twice that of steel, wood, plastics, and aluminum combined and is projected to exceed $600 billion in revenue by 2025. However, despite this large-scale use of concrete worldwide, the usage of concrete in India is comparatively new and came into existence in the past century. Let’s walk down a glimpse of concrete history in India!
History of Concrete in India
The majority of contemporary accounts in architectural and engineering journals on the use of reinforced concrete in India refer to its use in buildings, structures, and civil engineering works such as roads and bridges. It was also extensively employed for more mundane items such as a lamp and fence posts, and railway sleepers. There was also mention that India should build reinforced concrete ships for the coastal trade to save on imported steel. The following is a summary of buildings and engineering structures and other miscellaneous uses, selected to illustrate the various forms and applications of reinforced concrete.
Bridges
The earliest documented reinforced concrete structures in India found to date are two small bridges constructed in 1901 to designs by Major E. R. B. Stokes-Roberts, R.E.
Harbour Facilities
The Port of Madras was constructed over 1400 metres of wharfing between 1905 and 1910 using pre-cast piles and retaining walls that were driven into the sand. The wharf wall was anchored in place with steel ties that were encased in concrete for corrosion protection.
Water Tanks and Towers
The first recorded reinforced concrete water tanks were designed in the early 1900s by Major StokesRoberts.
Roads
The early concrete roads were unreinforced, such as the road over Law’s Bridge in Madras constructed in 1914 which is described as probably the oldest in India.
Housing
The first reinforced concrete buildings were also designed and built by Military Engineers and Stokes-Roberts is referred to as the engineer for the posts, beams, and rafters on an un-named army barrack constructed prior to 1905.
However, despite the usage of concrete in the 1900s, the use of concrete for construction in India came to a halt with the turmoil of British empire rule might come to an end in India. Hence, for many people who work with or study India’s building environment, the city of Chandigarh dating from the mid-1950 is often considered to be the starting point for the use of concrete reinforced concrete in India. By the time when Europe and North America have been performing construction using reinforced concrete for over a century. Thus, reflecting the late introduction of concrete in India.
Since the introduction of concrete for construction purposes in India, engineers and contractors have faced widescale challenges to maintain these concrete structures. The reason behind these challenges are the cracks in the concrete. These cracks happen from time to time, with many external factors playing a crucial role in it. Let’s walk you through why concrete cracks and the types of cracks that are usually seen with concrete.
Why Concrete Crack?
Concrete is a widely used construction material due to its strength, durability, and versatility. However, even the strongest concrete can crack due to various factors such as shrinkage, thermal expansion, overloading, and subgrade settlement. Different types of cracks can be seen on concrete structures such as plastic shrinkage cracks, drying shrinkage cracks, settlement cracks, overload cracks, etc. Identifying the type and cause of a crack is crucial in determining the appropriate repair method. Preventative measures such as proper mix design, reinforcement, and curing methods can also help reduce the likelihood of cracking. Understanding why concrete cracks and the different types of cracks can help ensure the longevity and safety of concrete structures. Let’s walk you through the 10 common types of concrete cracks and why it usually happens!
Common Types of Cracks in Concrete
When we see a crack in a concrete slab or wall, our first assumption is typically that something has been done wrong–but that’s not always the case. Actually, concrete cracks are very common, some are even inevitable.
According to American Concrete Institute touches on the issue of cracking concrete in their American Concrete Institute manual, ACI 302. 1-40: “Even with the best floor designs and proper construction, it is unrealistic to expect crack-free and curl-free floors. Consequently, every owner should be advised by both the designer and contractor that it is normal to expect some amount of cracking and curling on every project, and that such occurrences do not necessarily reflect adversely on either the adequacy of the floor’s design or the quality of its construction”
10 Common types of Concrete Cracks
Horizontal Concrete Cracks
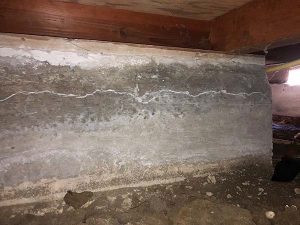
Horizontal cracks are most commonly encountered at beam and column junctions, as well as at the column face, where tensile stress is high.
Horizontal cracks in columns are caused by the following factors: insufficient moment resistance capacity, insufficient reinforcement, the effect of shear force, direct load, and uniaxial bending, and the placement of installed reinforcement.
If allowed to persist, horizontal cracks would reduce the shear strength of the column, posing a significant danger of structural failure. As a result, it demands prompt attention.
Corrosion Concrete Cracks
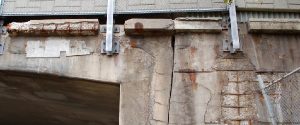
Corrosion cracks form primarily along the course of the concrete column reinforcement. Corrosion cracks are mostly the same width and usually get wider as they age.
The main cause of corrosion reinforcement in concrete columns is insufficient bonding between concrete and steel bars, as well as possible reinforcement corrosion.
Splitting Concrete Cracks
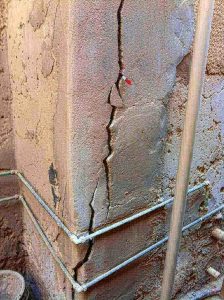
Split cracking appears as short parallel vertical cracks with non-uniform width on the concrete column face.
The insufficient load-bearing capacity of the column, an inadequate cross-section of the column to withstand the load action, insufficient steel reinforcing, and poor concrete quality can cause splitting fractures into concrete columns.
Diagonal Concrete Cracks
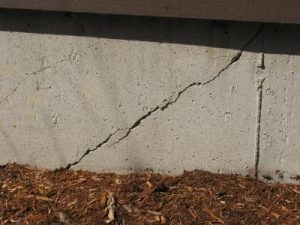
Diagonal cracks can appear anywhere along with the reinforced concrete’s height. These types of cracks always affect the entire concrete column face. Insufficient cross-section, insufficient load-carrying capabilities, and insufficient reinforcement steel are the most common causes of diagonal cracks in concrete columns.
Diagonal cracks must be repaired immediately since they might weaken the entire structure in a short period of time.
Plastic Shrinkage Concrete Cracks
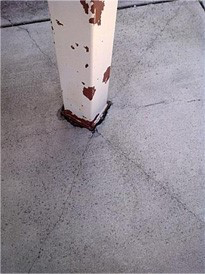
When concrete is still in its plastic state (before hardening), it is full of water. When that water eventually leaves the slab, it leaves behind large voids between the solid particles. These empty spaces make the concrete weaker and more prone to cracking. This type of cracking happens frequently and is referred to as “plastic shrinkage cracking”. While plastic shrinkage cracks can happen anywhere in a slab or wall, they almost always happen at reentrant corners (corners that point into the slab) or with circular objects in the middle of a slab (pipes, plumbing fixtures, drains, and manholes). Since concrete cannot shrink around a corner, stress will cause the concrete to crack from the point of that corner.
Plastic shrinkage cracks are typically very narrow in width and barely visible. While nearly invisible, it is important to remember that plastic shrinkage cracks don’t just exist on the surface, they extend throughout the entire thickness of the slab. An excessively wet mix is a contributing factor to shrinkage in concrete. While water is an essential ingredient in every concrete mix, there is such a thing as too much water. When the mix contains too much water, the slab will shrink more than if the correct amount of water was used. Hot weather is another big reason for plastic shrinkage cracks. Control joints can be incorporated into the slab to prevent shrinkage cracking. The joints will open up as the concrete slab gets smaller.
Expansion Concrete Cracks
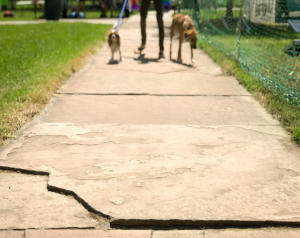
Just like a balloon, heat causes concrete to expand. When concrete expands, it pushes against anything in its way (a brick wall or adjacent slab for example). When neither has the ability to flex, the expanding force can be enough to cause concrete to crack.
Expansion joints are used as a point of separation (or isolation), between other static surfaces. Typically made of a compressible material like asphalt, rubber, or lumber, expansion joints must act as shock absorbers to relieve the stress that expansion puts on concrete and prevent cracking.
Heaving Concrete Cracks
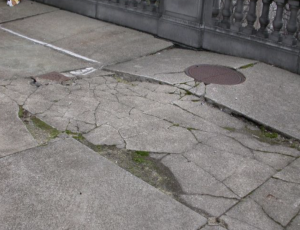
When the ground freezes, it can sometimes lift many inches before thawing and settling back down. This ground movement brought on by the freezing and thawing cycle is a huge factor contributing to concrete cracking. If the slab is not free to move with the ground, the slab will crack.
Large tree roots can have the same effect on a slab. If a tree is located too close to a slab, the growing roots can lift and crack the concrete surface. Always consider this when laying a slab.
Settling Concrete Cracks
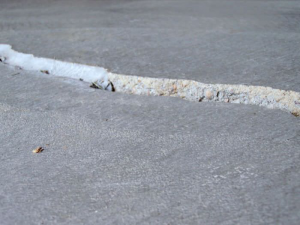
On the other hand, ground settling below a concrete slab can also cause cracking.
Settling cracks typically occur in situations where a void is created in the ground below the concrete surface. Think about when a large tree is removed from nearby and the roots begin to decompose or when a utility company digs a trench for their lines, pipes, etc. and don’t compact the soil when they refill it–these are examples of instances where settling cracks are likely to happen.
Concrete Cracks caused by Overloading the Slab
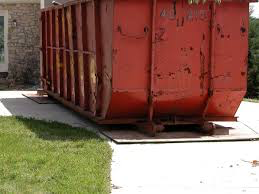
Although concrete is a very strong building material, it does have its limits. Placing excessive amounts of weight on top of a concrete slab can cause cracking. When you hear a concrete mix has a strength of 2000, 3000, 4000, or 5000+ PSI, it is referring to the pounds per square inch it would take to crush that concrete slab.
When it comes to residential concrete slabs, overload of the actual slab isn’t all that common. Instead, what is more likely to occur is excess overload on the ground below the slab. After a heavy rain or snowmelt when the ground below is soft and wet, excessive weight on the slab can press the concrete down and result in cracks. Residential homeowners who place large recreational vehicles or dumpsters on their driveways are more likely to see this type of cracking.
Concrete Cracks caused by Premature Drying
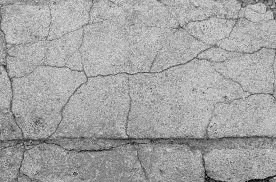
There are two common types of cracks brought on by premature drying.
Crazing cracks are very fine, surface cracks that resemble spider webs or shattered glass. When the top of a concrete slab loses moisture too quickly, crazing cracks will likely appear. While unsightly, crazing cracks are not a structural concern.
Crusting cracks typically happen during the concrete stamping process, which is a way of adding texture or pattern to concrete surfaces. On sunny or windy days where the top of the slab dries out quicker than the bottom, the top of the concrete surface can become crusty. When the stamp is embedded, it pulls the surface apart near the stamped joints and causes small cracks around the outside edges of the “stones”. Again, while they don’t look great, crusting cracks are not a structural issue to be considered about.
————————————————————————-
Now that we have a detailed view of the different types of concrete cracks in this segment of our blog with an in-depth understanding of why concrete generally cracks. In the upcoming segment of our blog, we will focus on how Sturdflex can help engineers and contractors with crack issues in concrete.
Analysis of Concrete Crack
It’s often difficult to determine exactly what caused a particular crack. Proper site preparation, a quality mix, and good concrete finishing practices can go a long way toward minimizing the appearance of cracks and producing a more aesthetically pleasing concrete project. To know more on how to achieve an aesthetically pleasing concrete project, tune in to the Sturdflex blog next week.